Revolutionizing 3D Printing with an Innovative 3D Printing Method for Sustainability
Innovative 3D printing method has transformed manufacturing by enabling highly customized objects such as hearing aids, dental implants, and intricate mechanical parts. However, traditional 3D printing techniques often produce substantial waste, mainly from support structures that are essential during printing but discarded afterward.
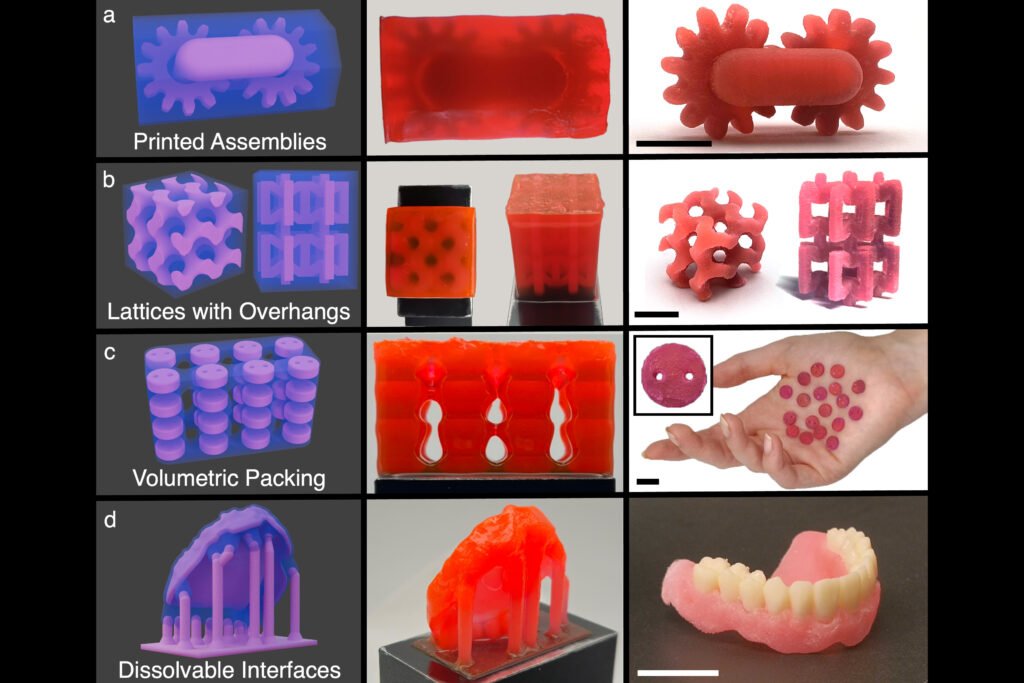
MIT researchers have now developed an innovative 3D printing method that not only fabricates complex, multipart designs but also drastically reduces waste. Their technique uses dissolvable support materials that can be easily removed and recycled. This breakthrough promises faster production, lower costs, and greater sustainability in additive manufacturing.
Understanding Vat Photopolymerization and Challenges in Conventional 3D Printing Methods
Vat photopolymerization (VP) is a common 3D printing method that uses patterned light to cure liquid resin layer by layer, creating detailed objects. However, the process requires support structures made from the same resin to hold overhangs and complex shapes during printing
After printing finishes, workers manually remove these supports, often clipping and filing them laboriously, which generates a significant amount of discarded material. Typically, the supports are not recyclable, creating environmental and economic concerns.
The Innovative 3D Printing Method: Dual-Phase Resin That Responds to Light
MIT engineers developed a novel resin that cures into two distinct types of solids depending on the wavelength of light it receives.
- Ultraviolet (UV) Light: Cures the resin into a robust, durable solid suitable for the final product.
- Visible light transforms the resin into a soft solid that dissolves easily in specific solvents.
This dual-phase behavior allows the main structure and its supports to be printed simultaneously in a single process. After printing, the supports dissolve in a safe solvent bath, freeing the finished part without manual intervention or waste.
How an Innovative 3D Printing Method Enables Sustainable Support Recycling
An outstanding feature of this method is the recyclability of the dissolved support material. The supports can dissolve in common, food-safe solvents like baby oil, or even in the original resin’s base liquid. This means the dissolved material can be filtered and reincorporated into fresh resin, creating a closed-loop system that minimizes waste and reduces material costs.
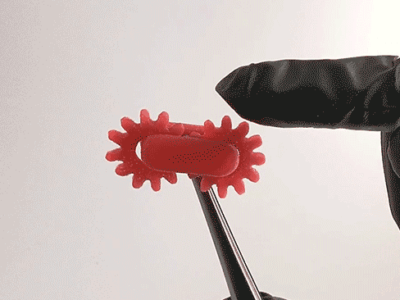
Such recycling capability is a major step toward sustainable 3D printing, aligning with global efforts to promote circular manufacturing practices.
Practical Applications: Printing Complex and Functional Assemblies
Using this innovative resin, the research team successfully printed a variety of intricate structures:
- Interlocking gears that demonstrate precise mechanical movement.
- Delicate lattice frameworks with complex internal geometries.
- Multipiece assemblies such as a ball trapped within a square frame.
- Fun and detailed models like a miniature dinosaur encased in a dissolvable support “egg.”
This capability to produce multipart functional objects with moving parts in a single print without manual support removal opens new avenues for custom medical devices, precision engineering components, and artistic models.
Overcoming Technical Challenges: Bridging Chemistry and Photopolymerization
Developing this dual-phase resin required sophisticated chemical engineering. Initially, UV-cured supports lacked sufficient strength due to partial polymer crosslinking from the weaker light sources in 3D printers compared to benchtop setups.
The solution involved adding a third “bridging” monomer to connect the two primary monomers, resulting in a tougher and more stable polymer network under UV light. This breakthrough ensured that the UV-cured main structures remain intact during the dissolution of visible light-cured supports.
Expert Insights: Perspectives from MIT Researchers
Graduate student Nicholas Diaco emphasized the practical benefits: “You can now print multipart functional assemblies with interlocking or moving components, and then simply wash away the supports. Instead of discarding the support material, you recycle it on site, drastically reducing waste.”
Professor A. John Hart, head of MIT’s Mechanical Engineering Department, highlighted the future potential: “We aim to expand this approach by developing new resins with customized mechanical properties and wavelength selectivity. Coupled with automated part handling and resin recycling, this could revolutionize polymer 3D printing at an industrial scale.”
The Future of Additive Manufacturing: Towards Resource Efficiency and Cost-Effectiveness
This innovative 3D printing method represents a critical step toward greener manufacturing. By integrating wavelength-selective resins and closed-loop recycling, it paves the way for:
- Reduced environmental impact through less material waste.
- Enhanced production speed by eliminating manual support removal.
- Lower overall costs by reusing support materials.
- The ability to fabricate highly complex and personalized products with minimal post-processing.
Continued research will focus on refining resin formulations, expanding printable materials, and scaling the technology for commercial use.
Supporting Research and Funding
This groundbreaking research was supported by prominent institutions, including the Center for Perceptual and Interactive Intelligence (InnoHK) in Hong Kong, the U.S. National Science Foundation, the U.S. Office of Naval Research, and the U.S. Army Research Office. The collaboration underscores the interdisciplinary effort behind advancing sustainable manufacturing technologies.